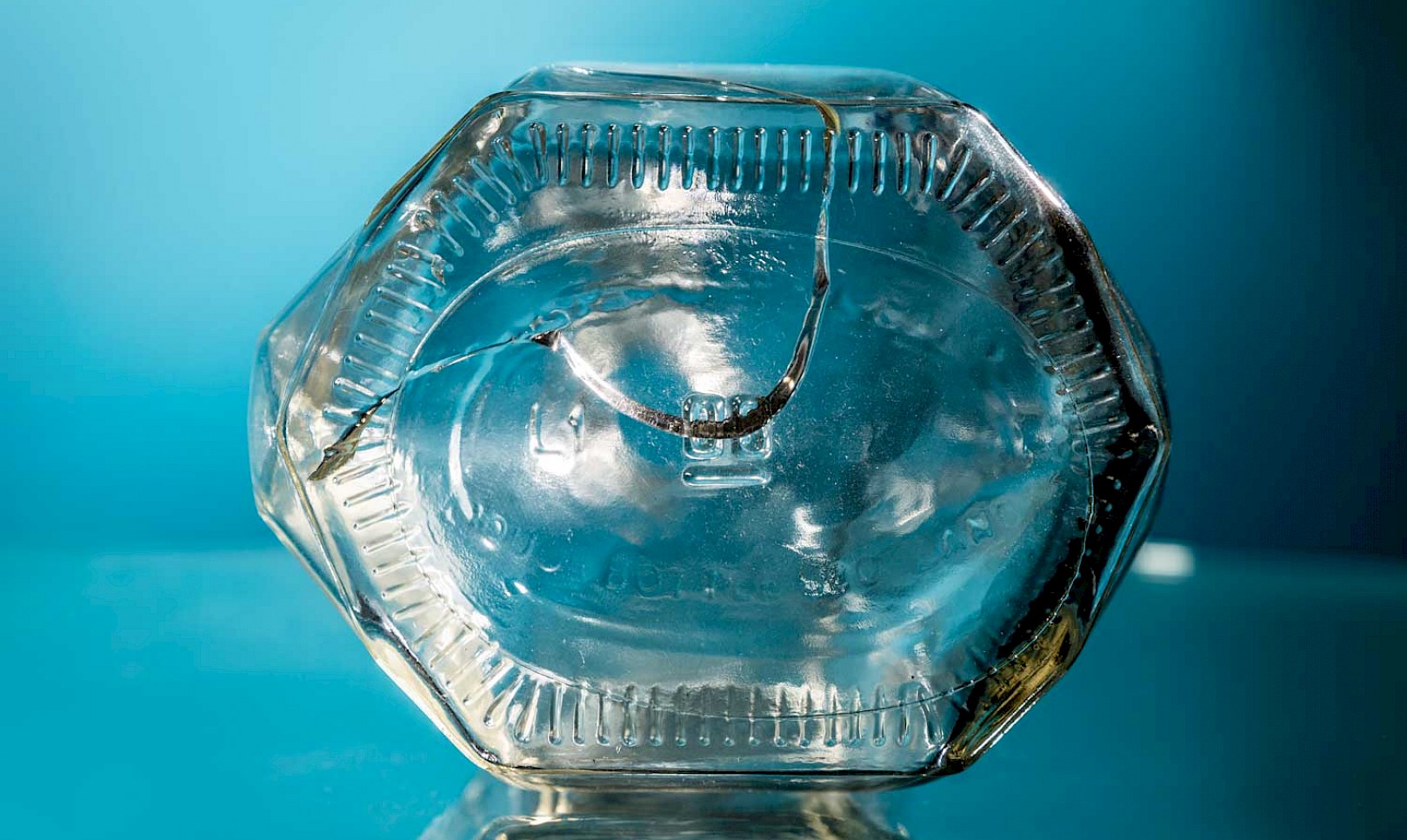
The breakage of glass can be dangerous and costly to manufacturers. However, it is not always simple to diagnose glass breakage and identify the cause of the problem.
Understanding glass breakage and fracture patterns can help you identify the origin of breakage and the root cause of product failure. This can eliminate future breakage issues and help resolve disputes.
In this blog, the technical glass experts from Glass Technology Services will cover everything you need to know about glass breakage patterns and glass failure analysis, including:
- An overview of glass strength
- The principles of glass breakage
- The different types of glass and their breakage patterns
- The importance of glass breakage patterns
- 6 types of glass breakage patterns
- How to identify the breakage origin
- 8 breakage origins caused by manufacturing defects
- 3 breakage origins caused by damage
Understanding glass strength
Glass is extremely strong unless it has a weakening defect or is damaged or scratched.
Theoretical glass strengths:
- Glass fibres: 2000+ MPa
- Pristine glass: 700 MPa
- Moulded glass: 300 MPa
- Light Scratches: 70 MPa
- Heavy Scratches: 35 MPa
Factors affecting glass strength
Many factors have an impact on the strength of glass. Here is a brief overview.
Surface condition:
- Scuffing
- Scratches
- Abrasion damage
Imperfections or defects:
- Inclusions
- Cord
- V-notches
- Undercuts
Internal stress:
- Poor annealing profile
- Poorly controlled heat working
Design:
- Shape
- Thickness
- Component interaction
The manufacturing process:
- Different mould types and forming methods
Principles of glass breakage
Glass breaks according to the fracture equation:
- STRESS + ORIGIN = FAILURE
Higher energy is required to break an item with a small origin damage/defect. However, breaking a glass item with a significant origin damage/defect takes less energy. Failure origins can take many different forms, which we will cover in more detail later on.
All glass breakages start from an origin, always on an interface (usually a surface). Glass will only fail under tension, even if the glass is exposed to additional forces. The fractures propagate at 90 degrees to the maximum tensile force.
Different types of glass and their breakage patterns
Residual stress remains in the glass after the forming process. Some processes strengthen glass, making it less likely to break.
Annealed glass
Annealing aims to reduce/remove the residual stress in the glass by holding the temperature and controlling the cooling process. When annealed glass breaks, it will shatter into sharp and potentially dangerous shards.
Toughened glass (safety glass)
Toughening increases the thermal strength of glass by introducing a compressive layer of stress at the surface. This is done by controlled cooling with air jets. Toughened glass is unlikely to break and has increased resistance to thermal stress. However, if it does break, it will shatter into tiny, harmless fragments with blunt edges.
Heat-strengthened glass
Heat-strengthened glass is also produced through controlled heating and cooling techniques, but the temperature is lower than toughened glass. Because of this, it will break into larger and sharper fragments.
Chemically toughened glass
Chemically Toughened glass is produced by exposing the glass surfaces to a potassium rich bath which, through the process of ion exchange causes a compressive layer at the glass surface.
Laminated glass
Laminated glass is made of two or more glass panels that are permanently bonded with interlayers.
The importance of glass breakage patterns
Interpreting breakage patterns and fracture markings allows you to:
- Identify the direction of fracture propagation.
- Assist in the reconstruction of the broken bottles.
- Assist in identifying the location of breakage origins.
- Identify distinct breakage stages, i.e. pauses and changes in direction.
- Help interpret breakage patterns and, ultimately, the forces involved in the breakage.
6 types of glass breakage patterns
Examining fracture and breakage patterns is a crucial part of glass failure analysis. These general principles apply to all types of glass flat containers, tradeware, tableware, and other types of glassware.
Surfaces need to be clean and dry to make markings visible, and good light is essential.
The prominence or severity of markings increases with the energy of failure:
- Low energy = faint markings
- High energy = strong markings
Markings on both sides of the fracture will identically match, which is crucial when reconstructing a broken sample.
1. Ripples
Ripples radiate outwards from the point of origin, common in high-force breakages. This type of fracture pattern is the primary way to identify the direction of travel in glass breakages.
2. Mirror grey hackle (or mirror mist hackle)
This is often associated with extremely high levels of force such as pressure failures. With mirror grey hackle, there will be an area that looks like highly polished glass and one that looks like etched or frosted glass. The term ‘hackle’ refers to the straight lines that travel in the direction of the breakage. This can be used to determine the direction of fracture propagation.
The size of mirror will depend on the amount of energy involved in the failure:
- Small mirror = high energy
- Large mirror = low energy
Mirror grey hackle is harder to identify than ripples and much less common.
3. Feathering
Feathering refers to the lines between the ripple marks, which tend to get bigger each time. This indicates that the crack is running out of energy and is a clear sign that you’re far away from the point of origin.
4. Cantilever curl
These are typically a result of bending forces on the glass, and the glass is unevenly loaded on one side. As the glass rotates around, the angle of the force changes, and so do the fractures. An example is the stem of a champagne glass broken through bending.
The result is the glass surface looks like it peels away from the side opposite the failure origin. Curved fracture surfaces can indicate which side was loaded and where the tension was induced.
5. Dwell marks
Dwell marks indicate a pause in fracture propagation. However, the duration of the pause is unknown and can not be determined.
Dwell marks usually feature:
- A prominent ripple mark
- Striations leading away from the ripple
- A change in fracture plane or direction
6. Striations
Striations are a series of linear marks that follow the direction of fracture propagation. They are sometimes associated with dwell marks.
How to identify the breakage origin
To recognise a breakage origin, you’ll need to look for the following indications:
- Fracture markings travel in opposite directions on the same piece of glass
- A disturbance in light reflection is present
- Usually, on an original surface of the glass
- Often present in a flatter region
8 breakage origins caused by manufacturing defects
1. Checks
- A fracture less than 6mm in length that penetrates the glass
2. Splits
- A fracture more than 6mm in length that penetrates the glass
3. Folds
- A fold is a crease or crevice in the glass's surface that is not directly visible to the naked eye. It is sometimes called a sharp seam.
- Folds often occur at any blank or finish seam on a container, but it is most common at the baffle or neck.
- A fold is a strength-reducing defect that may severely reduce a container's thermal shock and internal pressure strength.
4. Seeds and blisters
Bubbles, seeds and blisters are all gaseous inclusions in the glass.
- Blister. These are bubbles greater than 1mm in size. They can occur during melting and forming, these can occur due to causes such as contamination, electrolysis or entrapped air/carbon dioxide.
- Seed. These are bubbles less than 1mm, often formed in melting. Both seeds and blisters are usually categorised as visual imperfections and rarely result in breakage unless they are a significant size or are broken.
- Open bubbles. These are where the interior or external surface has been exposed. They can occur anywhere in a container, but when they occur on the internal surface, they are a critical defect as there is a risk of glass-in-product. Non-critical open bubbles are still strength-reducing defects.
5. V-notches
- These are caused by design features or embossing/engraving.
6. Inclusions (contamination within the glass)
- Inclusions can affect glass strength depending on their position and whether they are stress-raising.
7. Crizzle
- A surface fracture which reflects the light but does not significantly penetrate the glass.
8. Chatter marks
- Shallow surface fractures that are often caused by an abrasion or contact with the glass.
3 breakage origins caused by damage
1. Bruises
- This localised impact results in crushed and powdered glass.
2. Abrasions
- These are caused by blunt objects running over the glass surface, such as harsh glass-to-glass contact.
3. Scatches
- These result from sharp objects running over the glass surface, such as broken glass or knives.
How Glass Technology Services can help
Glass Technology Services offers a wide range of tailored services to support your unique needs and situation. Our team’s breadth of knowledge and unrivalled expertise in glass can help you understand the root cause of your glass breakage or failure.
Glass failure analysis
Our glass failure service is the best way to identify the root cause of any breakages and help you identify and resolve any issues with your manufacturing line. Glass failure (or fracture) analysis combines glass fractography and microscopy to diagnose and determine the true cause of product failure.
We analyse products spanning all sectors, including food and drink packaging, domestic glass, furniture, scientific glassware and pharmaceutical packaging. Our analysis requires that all the pieces of broken glass or glass fragments be retained to allow a full investigation to be conducted.
We investigate a range of product failures and related issues, including
- glass breakages and fracture diagnosis
- failure types – including those due to nickel sulphide inclusions, commonly referred to as ‘spontaneous glass failure’ or ‘spontaneous glass breakage’
- glass impacts and suspected vandalism
- thermal failures and thermal shock
- impact
- internal pressure
- vertical load
- product failures, cracking and fractures
- insulating glass unit failures
- component interactions
- fit for purpose analysis
Glass failure analysis course
If you’re looking for more in-depth information about glass breakage patterns and failure analysis, we offer a two-day technical course for glass technologists, quality assurance and product complaints professionals. Our glass experts will cover glass strength, damage, and an analytical approach to failure investigation in much more detail than this blog has been able to.
If you have any questions about what we offer, please contact our team. We will be happy to answer any questions you may have about glass breakage patterns.
Free webinar: how glass failure investigation can help solve quality issues
Watch the free webinar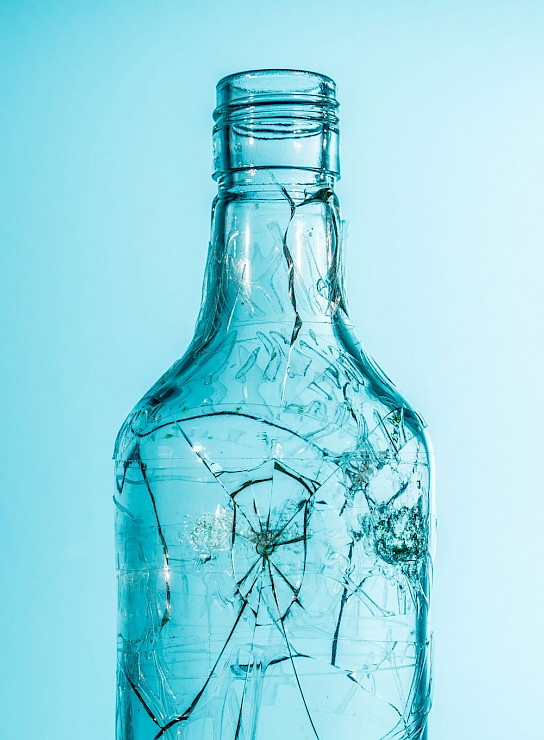