
News Article
Ebony Woodhall named Higher Apprentice of the Year at regional awards
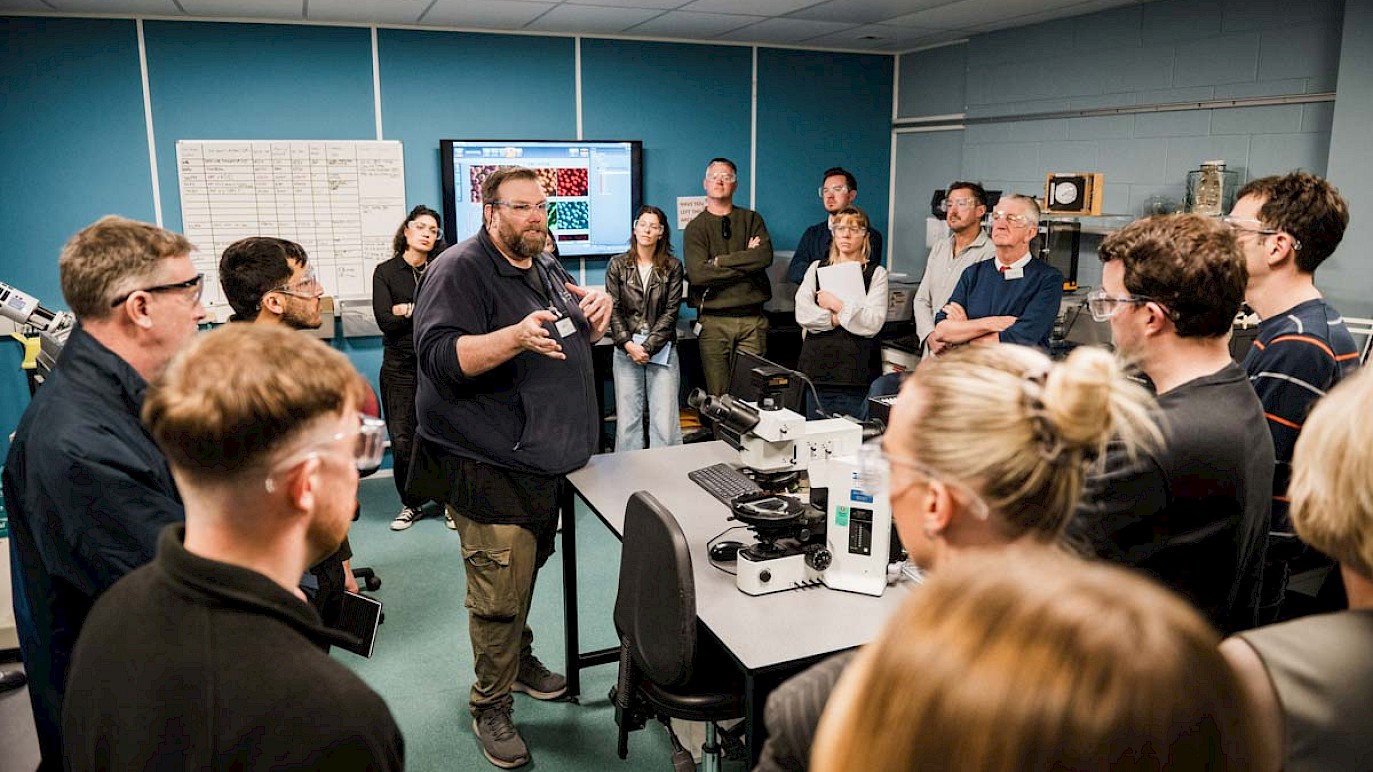
News Article
Attendees praise recent open day exploring innovative glass packaging and sustainability
We recently held a free event showcasing the future of glass packaging, aimed at brands and manufacturers who want to stay ahead of the curve.
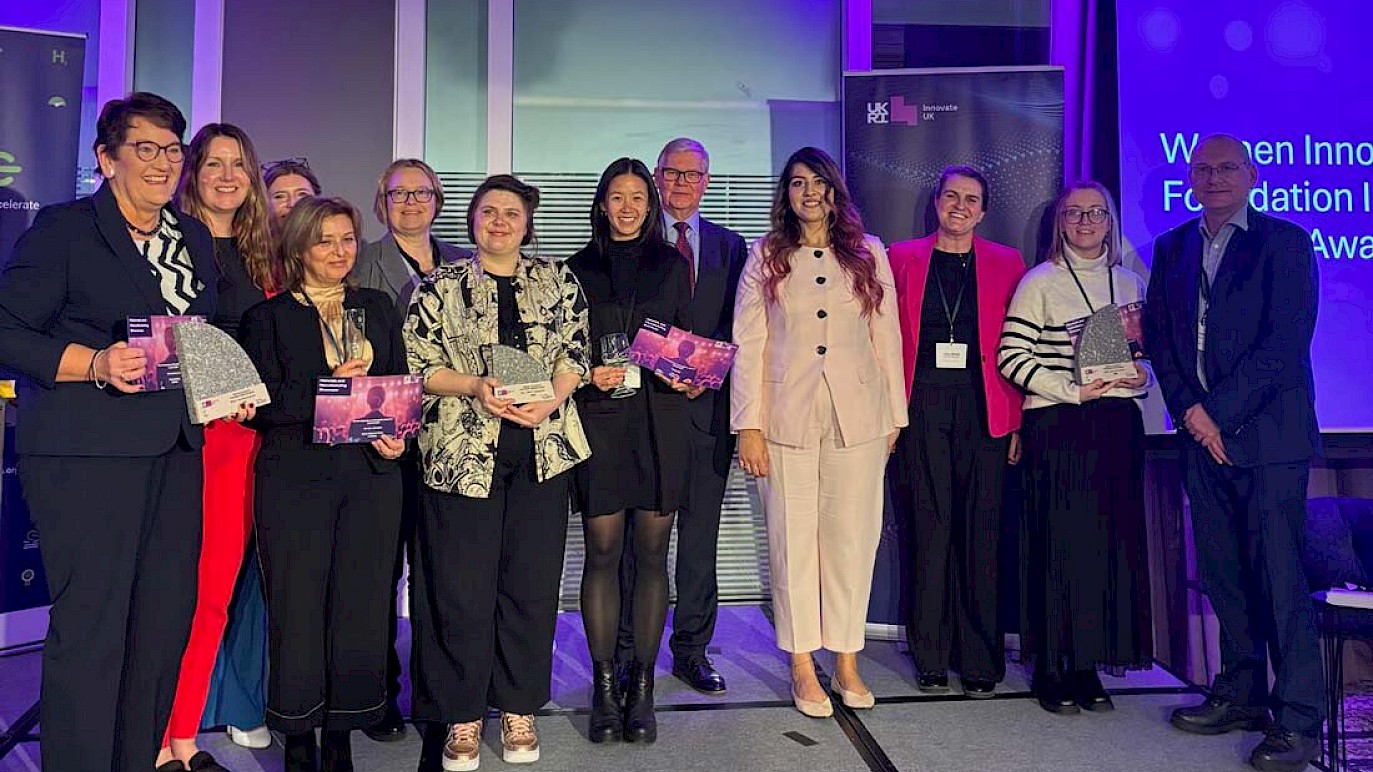
News Article
Glass Technology Services sponsors the Women Innovators in Foundation Industries Awards 2025
Glass Technology Services was delighted to sponsor the first Women Innovators in Foundation Industries Awards – supplying two unique glassware trophies from glass artist Lulu Harrison’s collaboration with glass blower Elliot Walker.
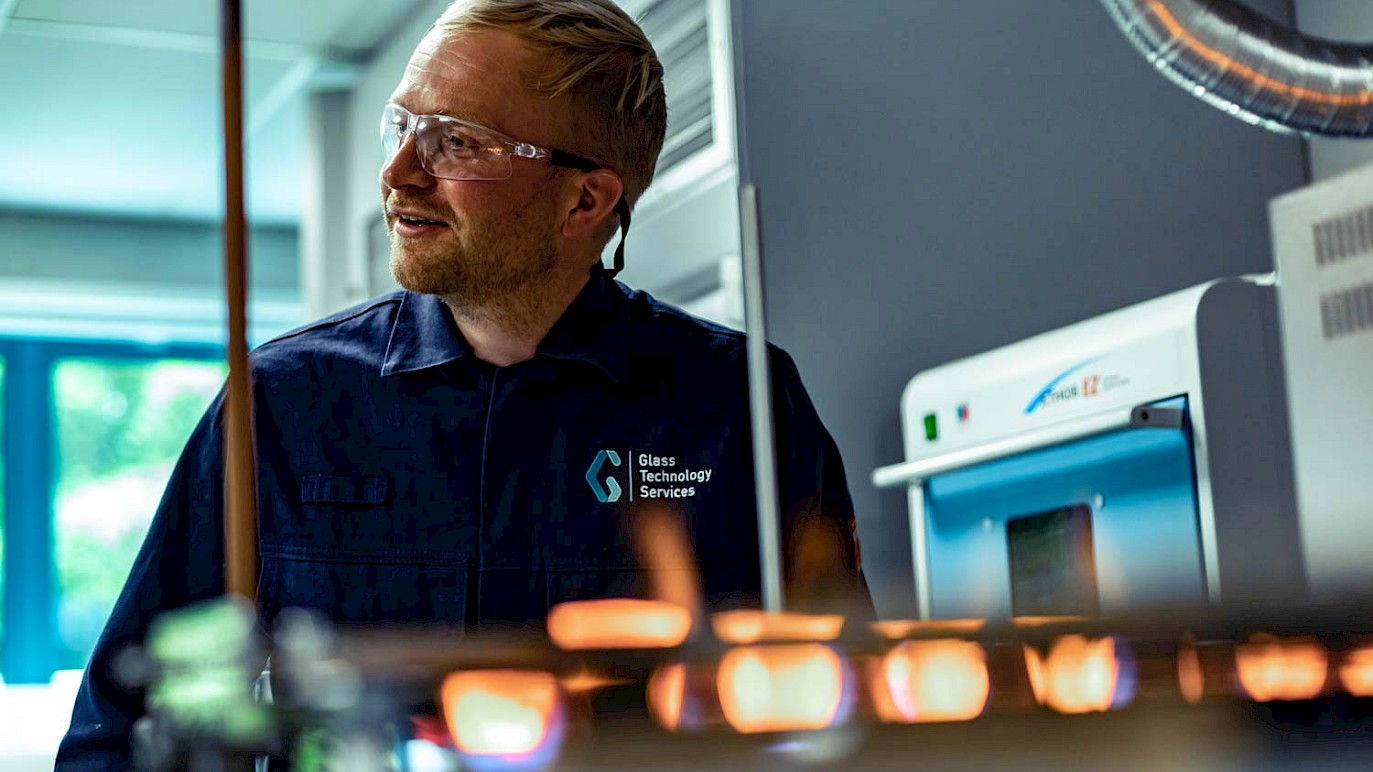
News Article
National Apprenticeship Week 2025
National Apprenticeship Week celebrates the incredible impact apprenticeships have on the people undertaking them, the organisations they work for, and the economy as a whole. In honour of this year’s event, we caught up with a few of our apprentices to find out more about their experiences.
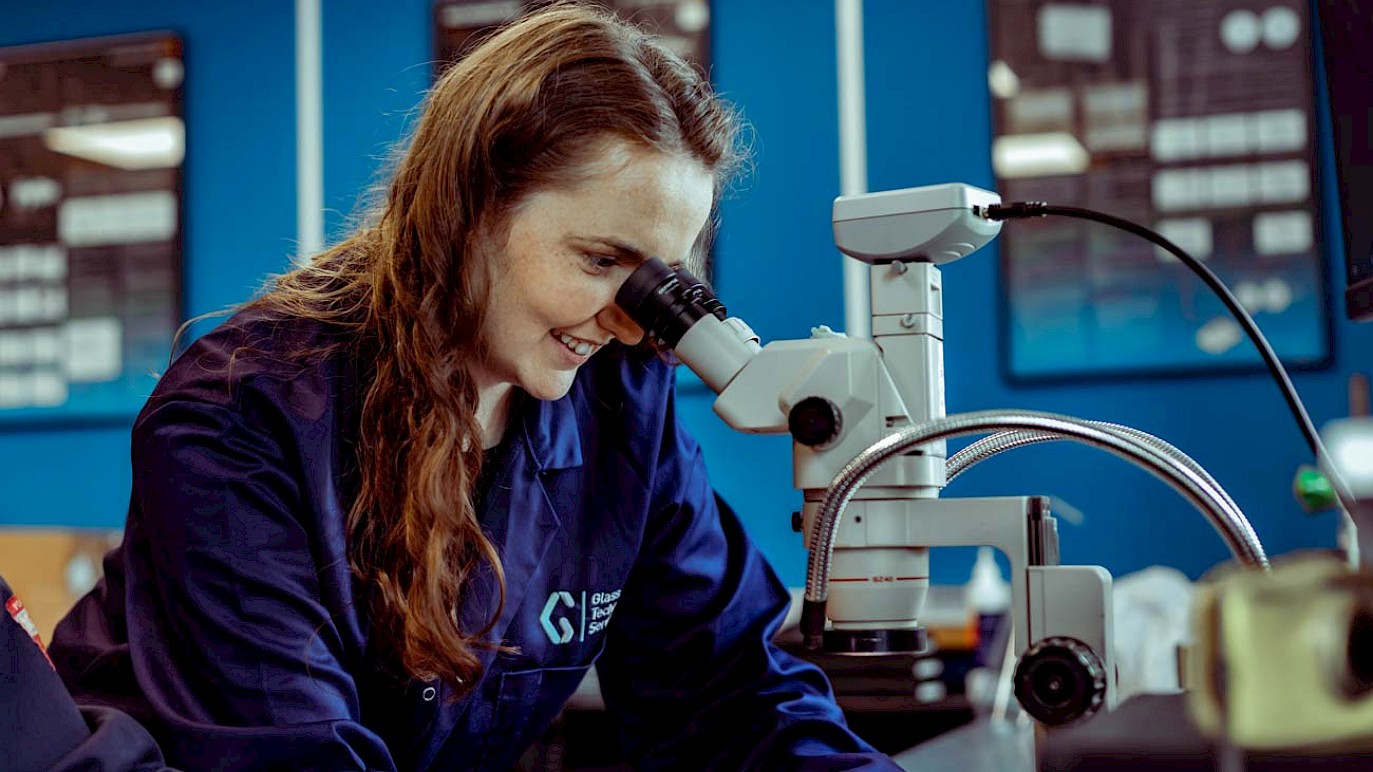
News Article
Inside perspectives for International Day of Women and Girls in Science
International Day of Women and Girls in Science – now in its tenth year – celebrates the incredible contribution that women and girls make to the world of science. We asked our own women in science to share their unique experiences of being female in a previously male-dominated field.
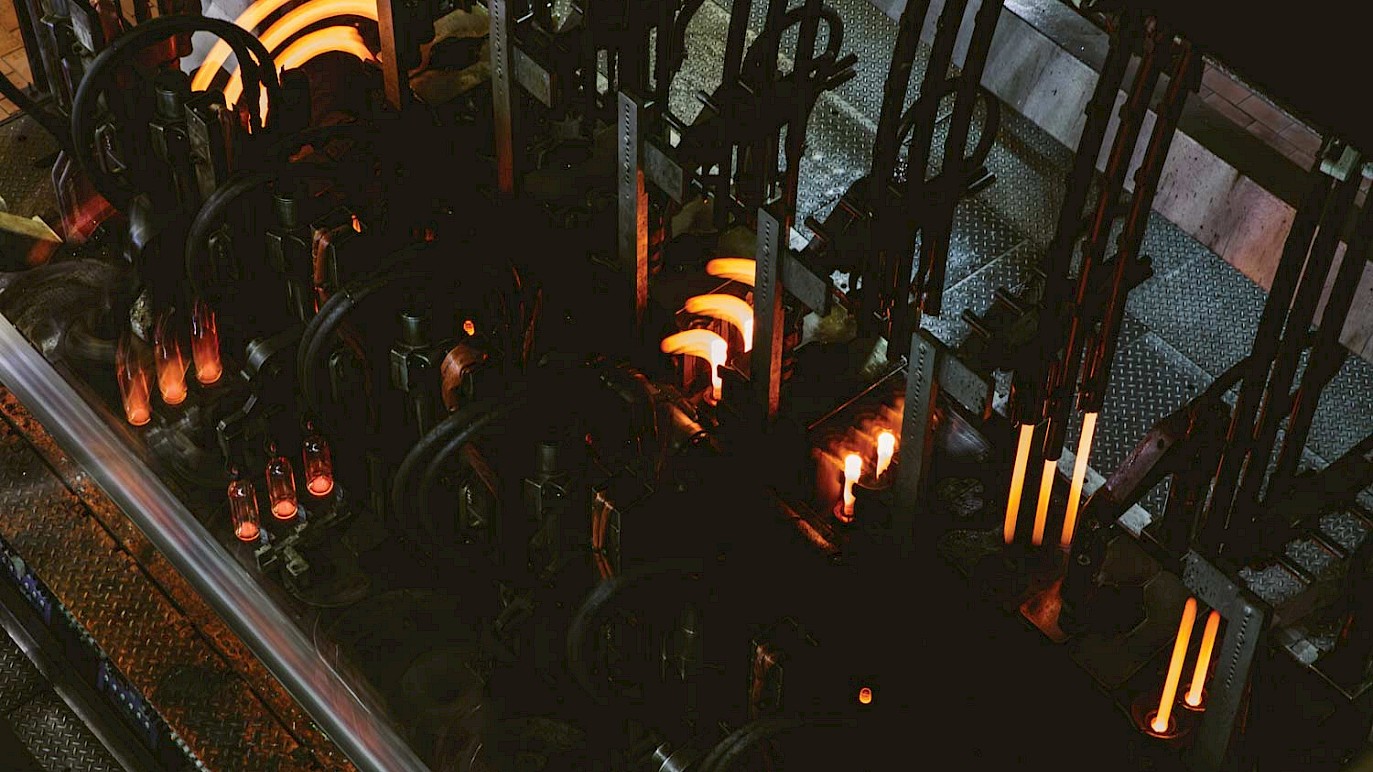
News Article